Plan utrzymania sieci elektrycznych w przedsiębiorstwie. Warunki utrzymania TP. Oszacowanie stanu technicznego tp
Obecnie najczęściej stosowane są fabryczne kompletne rozdzielnice (KRU) o napięciu 3-10 kV.
Personel obsługujący stacjonarny KRU serii KSO-272, KSO-366, K-XII, KRU2-10 musi znać przeznaczenie poszczególnych części KRU i ich wzajemne oddziaływanie podczas pracy. Podczas serwisowania rozdzielnicy należy kierować się nie tylko PTE i PTB, ale także instrukcjami dotyczącymi rozdzielnicy i zainstalowanego w nich sprzętu.
Podczas oględzin zwraca się uwagę na: stan pomieszczeń (sprawność drzwi, wentylacja, ogrzewanie, zaparcia); sprawność sieci oświetleniowej i uziemiającej; dostępność sprzętu zabezpieczającego; poziom oleju w cylindrach przełącznika; stan izolacji, napędów, mechanizmów blokowania odłączników, pierwotnych styków odłączających, mechanizmów wykończeniowych; stan połączeń kontaktowych; obecność smaru na częściach trących mechanizmów; niezawodność połączenia rzędów zacisków, przejścia obwodów wtórnych do drzwi; szczelność połączeń stykowych obwodów wtórnych; działanie lokalnych przycisków sterujących przełączników.
Cała izolacja rozdzielnicy jest zaprojektowana na napięcie 10 kV, a przy pracy przy 6 kV ma podwyższoną niezawodność. Podczas obsługi rozdzielnicy zabrania się odkręcania zdejmowanych części szafy, podnoszenia i otwierania automatycznych żaluzji rękami w obecności napięcia.
Sprawdzanie przydatności pomieszczeń rozdzielnicy, drzwi i okien; brak przecieków w dachu i podłogach; sprawność zamków, sprzętu zabezpieczającego, ogrzewania, wentylacji, oświetlenia, uziemienia; poziom i temperatura oleju w aparacie, brak w nich wycieków; styki, izolacje (pęknięcia, zapylenie itp.), szyny produkowane są bez wyłączania rozdzielnicy:
1 raz dziennie - w obiektach ze stałym personelem dyżurnym;
przynajmniej raz w miesiącu - w obiektach bez stałego personelu dyżurnego;
co najmniej 1 raz na 6 miesięcy - w rozdzielnicy połączonej z podstacjami transformatorowymi.
W rozdzielnicy wysuwnej do pracy wyłącznik jest wyłączany przez odłączniki wbudowane w rozdzielnicę, linia odpływowa jest uziemiona, wózek ustawiany jest w pozycji naprawy, a dolne styki rozłączające są sprawdzane pod kątem braku napięcia. Następnie należy włączyć uziemnik i ustawić wózek w pozycji testowej (jeśli nie ma potrzeby pracy wewnątrz szafy). Wymiana bezpieczników w pomocniczej szafie transformatorowej odbywa się przy odłączonym obciążeniu.
Rozwinięcie wózka z wyłącznikiem i ustawienie go w pozycji roboczej to operacje odłączenia i umożliwienia połączenia; dokonują ich wyłącznie osoby dokonujące zmiany operacyjnej lub pod ich kierownictwem. Wózek można ustawić w pozycji roboczej tylko wtedy, gdy uziemnik jest odłączony.
W szafach rozdzielczych, w których połączenie obwodów wtórnych wózka wysuwnego z obudową realizowane jest za pomocą złącza wtykowego, dla prawidłowego usytuowania wkładu w stosunku do bloku montuje się go tak, aby połączenie wtykowe znajdowało się na stronę frontu szafki i do niej. Na wkładce i bloku zastosowano czerwone zagrożenia. Gdy złącze jest w pełni dopasowane, nakrętka łącząca jest wkręcana, aż pozostanie jeden obrót złącza. W tym przypadku szpilka wchodzi do gniazda na około 6 mm, co zapewnia niezawodne połączenie złącza. Eksploatacja wyposażenia szafy rozdzielczej odbywa się zgodnie z instrukcjami producentów.
Konserwacja rozdzielnicy o napięciu do 1000 V
W chwili obecnej szeroko rozpowszechnione są rozdzielnice wykonane z jednokierunkowych tablic konserwacyjnych Shch070. W nomenklaturze Shch070 znajdują się panele liniowe, wprowadzające, przekrojowe, specjalne i kombinowane. Strony łączące panele są takie same. Kiedy panele są montowane w osłonę, wolne końce ją zamykają.
Oprócz paneli Shch070, panele pomocnicze PSN, punkty zasilania z bezpiecznikami SP i SPU, punkty dystrybucji z wyłącznikami automatycznymi serii PR-21 i PR-9000, szafy z wyłącznikami automatycznymi Electron, szafy zasilające ShS, szafy przekaźnikowe ShR itp. stosowane są instalacje to specjalnie wykonane szafy wlotowe ShV, urządzenia rozdzielające wejścia ASU, osłony z maszynami instalacyjnymi SU-9400 oraz różne osłony grupowe i podłogowe. Zestaw wyposażenia paneli i szafek jest zróżnicowany i wyświetlany w standardowych siatkach schematów wypełnienia.
Inspekcję rozdzielnicy na napięcie do 1000 V przeprowadza się nie rzadziej niż raz na 3 miesiące lub w terminach określonych przepisami miejscowymi. Podczas konserwacji rozdzielnica jest sprawdzana i oczyszczana z brudu i kurzu oraz sprawdzana jest zgodność rzeczywistych warunków pracy urządzeń z ich nominalnymi parametrami technicznymi.
Aby oczyścić urządzenie z brudu, zdejmij obudowę lub pokrywę i przedmuchaj kurz sprężonym powietrzem. Plamy z sadzy i oleju usuwa się ściereczką zwilżoną benzyną lakową lub benzyną.
W przypadku metalowych obudów i obudów aparatów sprawdzane są punkty uziemienia oraz dokręcenie śrub lub nakrętek.
Sprawdzane są również mocowania połączeń stykowych w urządzeniach. Styki, które mają przebarwienia, utlenienie lub ciemnienie są demontowane, czyszczone papierem ściernym lub pilnikiem igłowym do metalicznego połysku, montowane i dokręcane. Sprawdź powierzchnie styku noży i ostrzy noży. Kilkakrotne włączanie i wyłączanie noży usuwa ślady tlenków z powierzchni styku. Miejsca spalania, napływy i odpryski metalu czyści się pilnikiem z drobnym nacięciem. Sprawdź wejście noży do szczęk. Noże muszą wchodzić jednocześnie, bez zniekształceń, na pełną szerokość suwu. Przekrzywienie noży eliminuje się poprzez dokręcenie śrub mocujących. Za pomocą sondy 0,05 mm sprawdzić stopień kontaktu noży z gąbkami. Sonda powinna wejść na nie więcej niż U2 powierzchni styku.
Jeśli pasowanie jest luźne, można je wyeliminować przez zgięcie gąbki lub wymianę sprężyny stykowej. Jeśli przełączniki nożowe mają specjalne noże, sprawdź stan ich sprężyn. Uszkodzone sprężyny są wymieniane.
Sprawdź izolację przewodów obwodów mocy i wtórnych urządzeń przełączających. Uszkodzone odcinki przewodów izolujemy taśmą izolacyjną. W przypadku uszkodzenia rdzenia miedzianego przewodzącego przewody wymieniane są na nowe lub lutowane lutem POS-ZO lub POS-40, w przypadku uszkodzenia rdzenia aluminiowego przewody wymieniane są na nowe.
Części uszczelniające aparatu są sprawdzane, uszkodzone wymieniane na nowe.
Rozrusznik magnetyczny jest włączany ręcznie, są przekonani o swobodnym ruchu układu ruchomego, obecności kontaktu między stykami ruchomymi i stałymi, braku przeniesienia układu stykowego, przydatności sprężyn stykowych. Sprężyny, które utraciły swoje właściwości elastyczne lub uległy uszkodzeniu, są wymieniane.
Kilkakrotnie włącz i wyłącz ręcznie wyłącznik. Szybkość włączania i wyłączania przełącznika nie powinna zależeć od szybkości ruchu klamki lub przycisków. Mechanizmy zawiasów smarowane są olejem narzędziowym.
Po każdym odłączeniu prądu zwarciowego maszyny instalacyjne są przeglądane ze zdjętą pokrywą, nie czekając na kolejny przegląd. Nie wolno bez potrzeby zdejmować osłony maksymalnego zwolnienia. W zwalniaku nie ma możliwości przestawienia śrub regulacyjnych, wygięcia lub opiłowania elementów bimetalicznych itp. W normalnych warunkach wyłącznik należy co 6 miesięcy sprawdzać ze zdjętą pokrywą.
Podczas kontroli komór łukowych rozruszników magnetycznych i wyłączniki, sadzę usuwać ściereczką nasączoną benzyną lakową lub benzyną. Metalowe plamy na siatkach dejonowych są usuwane za pomocą pilnika igłowego.
Mierzona jest grubość warstwy ceramiczno-metalowej styków. Jeżeli grubość warstwy ceramiczno-metalowej jest mniejsza niż 0,5 mm, styki są wymieniane.
Sprawdź cewkę rozrusznika magnetycznego, upewnij się, że nie ma uszkodzeń zewnętrznej powłoki uzwojenia, a także nieszczelności powłoki nawierzchniowej w wyniku przegrzania. Sprawdź szczelność cewki na rdzeniu.
Schematy pomiaru izolacji megaomomierzami:
a - włączenie megaomomierza M4100/5; b - М4100/1-4 na granicy „ML”; c - 410/1-4 na granicy „KL”; d - M4100/5 na granicy "MP"; d- M4100/5 na granicy „KL”
Sprawdź stan układu magnetycznego i zwartej cewki. Powierzchnie stykowe obwodu magnetycznego są czyszczone środkiem czyszczącym. Korozja na innych powierzchniach obwodu magnetycznego jest usuwana papierem ściernym i pokrywana schnącym na powietrzu lakierem. Sprawdź element grzejny. W przypadku wypaczenia, przepalenia metalu lub zwarcia cewek element należy wymienić. Płytka bimetaliczna jest wymieniana w przypadku odkształcenia i spalenia. Po wymianie Element grzewczy lub płytka bimetaliczna, przekaźnik jest podłączony do urządzenia lub obwodu, który umożliwia płynną regulację wartości prądu testowego.
Następnie sprawdź części izolacyjne rozruszników magnetycznych przełączników automatycznych, przełączników wsadowych i przełączników nożowych. Sprawdź, czy nie ma wiórów ani pęknięć. Na przełącznikach nożowych ślady spalenia lub wyładowania łukowego na płytach izolacyjnych są czyszczone papierem ściernym i pokrywane warstwą lakieru bakelitowego lub kleju BF-2.
Rezystancja izolacji instalacji elektrycznych rozdzielnicy jest mierzona megaomomierzem na czas i poza kolejnością w przypadku wykrycia wad. Pomiary wykonuje się w odcinkach lub odcinkach sieci, oddzielonych dwoma sąsiednimi bezpiecznikami; za ostatnim bezpiecznikiem, po uprzednim usunięciu z niego topliwego łącznika; między fazą a ziemią, a także między dwoma przewodami fazowymi.
Podczas pomiaru w obwodach mocy odbiorniki elektryczne, urządzenia, urządzenia są wyłączone, w obwodach oświetleniowych lampy są odkręcone, oraz gniazda wtykowe, przełączniki i tablice rozdzielcze pozostają podłączone.
Przed pomiarem rezystancji instalacji elektrycznych są one rozładowywane, to znaczy dotykane kolejno uziemionym przewodem każdej fazy, wykluczając możliwość uszkodzenia pracowników przez resztkowy ładunek pojemnościowy. To samo rozładowanie odbywa się po pomiarze.
Megaomomierze wykonane są na napięcie 500, 1000 i 2500 V. Urządzenie posiada trzy zaciski: 3 (masa), E (ekran), L (linia). Aby zwiększyć dokładność pomiaru, jeśli to konieczne, przyłóż elektrodę ekranową do izolacji i przymocuj ją do zacisku E.
Aby sprawdzić obecność lub brak napięcia w rozdzielnicy, określ przewód neutralny i fazowy, użyj wskaźnika napięcia UNN-10 lub IN-92 (ryc. 17.6, a). W celu wykrycia przepalonego lub zamkniętego bezpiecznika rurkowego wskaźnik należy podłączyć w sposób przedstawiony na ryc. b a aby sprawdzić poprawność uziemienie ochronne lub zerowanie - jak pokazano na rys. w. Fazowanie przewodów za pomocą wskaźnika odbywa się jak pokazano na ryc. G.
Techniczny konserwacja podstacji transformatorowej,(TP) i naprawa to główne rodzaje prac operacyjnych, które są wykonywane w TP.
Konserwacja podstacji transformatorowej jest obowiązkowa i ma na celu przeprowadzenie zestawu środków mających na celu utrzymanie sprawności sprzętu, ochronę elementów podstacji przed przedwczesnym zużyciem, a także przywrócenie charakterystyk i parametrów operacyjnych.
Konserwacja podstacje transformatorowe odbywa się zgodnie z zaplanowaną procedurą identyfikacji i eliminacji uszkodzeń i usterek. Jednocześnie uszkodzenia podstacji transformatorowej i jej elementów grożące skutkami (bezpieczeństwo ludności, zagrożenie pożarem itp.) muszą być usuwane natychmiast, jak najszybciej po wykryciu.
Warunki utrzymania TP
Należy zaplanować czynności związane z przeglądem technicznym i konserwacją TP. W tym celu zaleca się przedstawienie planu pracy:
- Wieloletni plan konserwacji z harmonogramem konserwacji na 6 lat;
- Harmonogram konserwacji na okres jednego roku;
- Harmonogram wyłączeń TP na miesiąc.
Przykład instalacji licznika elektrycznego
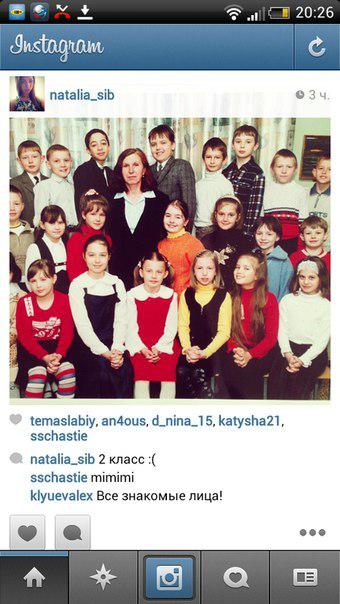
Każdy przegląd lub praca w TP przewiduje sporządzenie protokołu napraw i konserwacji, wraz z wypełnieniem karty prac naprawczych.
W celu oszczędzania zasobów, konserwacja stacji transformatorowych, optymalnie połączone z pracą na liniach wychodzących 0,38 kW.
Zespół zajmujący się scentralizowaną obsługą TP musi być wyposażony w pojazdy, mechanizmy i urządzenia takielunku, niezbędne narzędzie i środki ochrony. Ponadto ekipa naprawcza musi posiadać zaplecze komunikacyjne, dokumentację techniczną i całą listę opisy stanowisk pracy zapewnienie bezpieczeństwa w produkcji pracy.
Podczas wykonywania napraw, renowacji i innych środków nieautoryzowane zmiany w projekcie podstacji transformatorowych są niedozwolone. Wszelkie zmiany techniczne, które są wprowadzane do projektu TP, nie powinny zmniejszać wydajności, ponadto te same zmiany są wprowadzane decyzją głównego inżyniera.
Koszt utrzymania stacji transformatorowych
Podczas naprawy TP jest kompilowany umowa na utrzymanie stacji transformatorowej, zapewnienie realizacji prac prewencyjnych i naprawczych. Koszt utrzymania stacji transformatorowych ustalana jest na podstawie stanu procesu technologicznego, po wykonaniu procedury oceny jego stan techniczny.
Z reguły koszty utrzymania sprzętu elektrycznego znajdującego się w bilansie każdego przedsiębiorstwa są zbyt wysokie: jeśli przedsiębiorstwo nie jest podstawową działalnością, utrzymanie kadry wykwalifikowanych pracowników z wymaganym dostępem do sprzętu elektrycznego jest zbyt kosztowne .
Konserwacja rutynowa powinna być wykonywana na bieżąco przez wysoko wykwalifikowanego specjalistę zdolnego do zapewnienia wymaganej jakości pracy.Firma 10 Kilovolt oferuje naszym partnerom możliwość skorzystania z wiedzy naszych pracowników, którzy nie tylko mają dostęp do pracy z urządzeń napięciowych, ale także wymagane doświadczenie w konserwacji, rozruchu i przeglądach stacji transformatorowych.
Możemy zapewnić pełen zakres usług w zakresie utrzymania sieci elektrycznych oraz eksploatacji podstacji transformatorowych. Na niezawodność sprzętu składają się nie tylko rozwiązania techniczne i zastosowanie nowoczesnych materiałów. Wysokiej jakości konserwacja sprzętu podejście systemowe i umiejętności specjalistów - gwarancja wydajności i długiej żywotności każdego sprzętu.
Wideo: konserwacja podstacji transformatorowych
Zasady operacja techniczna instalacje elektryczne odbiorców, okresowe kontrole, kontrole i pomiary rezystancji izolacji przewodów elektrycznych są dostarczane w terminach ustalonych w przedsiębiorstwach w zależności od warunków pracy.
Podczas przeglądów paneli, zespołów i szaf sprawdzają, czyszczą i dokręcają połączenia stykowe urządzeń sterujących, sprawdzają stan połączeń stykowych w miejscu podłączenia kabla, zakończenia oraz obecność w nich masy kablowej, stan pancerz, izolacja i uziemienie kabla. W razie potrzeby masa kabla jest dodawana do lejków, przywieszki są wymieniane, lejki i metal pancerza kabla są malowane. Zwrócono uwagę na stan uziemienia korpusu osłony. W przypadku znalezienia uszkodzonych izolatorów lub szczęk bezpiecznikowych, są one wymieniane na nowe.
Podczas kontroli przewodów napowietrznych sprawdzają zwis przewodów, odległość między przewodami i ich odległość od ziemi, stan izolacji zewnętrznej, urządzenia izolacyjne (przepusty, izolatory, zaciski, lejki) w przejściach przez ściany i stropy , zapięcia z drutu. Zwraca się uwagę na użyteczność tulei izolacyjnych w punktach wejścia przewodów do metalowych skrzynek lub rur, na obecność dodatkowej izolacji na przecięciu przewodów elektrycznych. Sprawdzana jest obecność nakładek izolacyjnych na połączeniach przewodów w skrzynkach połączeniowych i podkładek ograniczających na połączeniach stykowych jednoprzewodowych przewodów przewodów do urządzeń i urządzeń.
Rezystancję izolacji przewodów elektrycznych mierzy się podczas głównych napraw nie rzadziej niż raz na 3 lata. W trakcie napraw bieżących oraz pomiędzy naprawami pomiary wykonywane są w terminach ustalonych zgodnie z lokalnymi warunkami eksploatacji.
Jeśli odcinek sieci elektrycznej był z jakiegoś powodu bez napięcia przez ponad miesiąc, to przed włączeniem jest sprawdzany i mierzona jest rezystancja izolacji.
Pomiar rezystancji izolacji w sieciach elektroenergetycznych i oświetleniowych wykonywany jest megaomomierzem na napięcie 1000 V z odłączonymi odbiornikami elektrycznymi, aparaturą i przyrządami oraz wyjętymi bezpiecznikami. Rezystancja izolacji między dowolnym przewodem a uziemieniem lub między dwoma przewodami musi wynosić co najmniej 0,5 MΩ.
Pomiary kontrolne napięć i obciążeń w poszczególnych punktach instalacji elektrycznej przeprowadzane są według specjalnego harmonogramu co najmniej 1 raz na 3 lata. Na podstawie tych pomiarów obliczane są straty w sieciach i opracowywane są środki mające na celu oszczędność energii elektrycznej i, jeśli to konieczne, podjęcie decyzji o wymianie przewodów.
Awarie lub naruszenia muszą być natychmiast usuwane. W przypadku braku możliwości usunięcia usterek podczas przeglądów, są one odnotowywane w dzienniku przeglądów, zgłaszane osobie odpowiedzialnej za instalacje elektryczne i usuwane przy kolejnych bieżących lub większych naprawach.
Utrzymanie linii kablowych
Niezawodność działania linie kablowe zapewnia wdrożenie zestawu środków (przeglądy, naprawy, testy prewencyjne). Na każdą linię kablową wpisywany jest paszport zawierający dane techniczne, w którym na bieżąco wprowadzane są w trakcie eksploatacji informacje o naprawach, testach i eksploatacji linii.
Nadzór nad stanem tras i kabli polega na wykonywaniu okresowych obchodów i przeglądów. Terminy inspekcji tras kablowych układanych w ziemi, tuneli i kolektorów ustalane są zgodnie z lokalnymi instrukcjami (jednak nie rzadziej niż raz na 3 miesiące). Studnie kablowe sprawdzane są co najmniej raz na 6 miesięcy, zakończenia dla napięć powyżej 1000 V - raz na 6 miesięcy, a dla napięć do 1000 V - raz w roku. Sprawdzają przydatność tulejek końcowych, powłoki antykorozyjne, temperaturę nagrzewania powierzchni kabli, oznakowanie, ochronę przed uszkodzeniami mechanicznymi, obecność wgnieceń w pancerzu itp.
Maszyny do robót ziemnych mogą pracować w odległości co najmniej 1 m od kabli. Młoty pneumatyczne do spulchniania gleby nad kablami są używane do głębokości nie większej niż 0,4 m, gdy kabel jest zakopany na więcej niż 0,7 m. Aby uniknąć uszkodzenia kabla, grubość warstwy gleby między kablem a źródłem ciepła musi wynosić co najmniej 25 cm.
Wszelkie usterki i naruszenia stwierdzone podczas przeglądów i kontroli tras kablowych są odnotowywane w dzienniku usterek i zgłaszane kierownikowi technicznemu. Uwagi te są eliminowane w zależności od nakładu pracy w celu ich wyeliminowania (natychmiast lub uwzględnione w planie remontu).
Niezawodność linii kablowej w dużej mierze zależy od temperatury nagrzewania elementów kabla podczas pracy. Po podgrzaniu powyżej dopuszczalnej temperatury pogarszają się właściwości elektryczne i mechaniczne izolacji kabla. przez długi czas dopuszczalne temperatury przewody nie mogą przekraczać: dla kabli z izolacja papierowa napięcie do 1 kV - 80 C, dla kabli o izolacji papierowej na napięcie do 10 kV - 60° C, dla kabli o izolacji gumowej i PCV - 65° C.
Dopuszczalne obciążenia prądowe kabli zależą od sposobu ułożenia kabla (w tunelach, w ziemi). Obliczone dopuszczalne obciążenia są wpisywane do paszportu linii kablowej.
Niezawodność linii kablowej w dużej mierze zależy od stanu osłony kabla. Jeśli jego szczelność zostanie naruszona, powietrze i wilgoć wnikają do kabla, co prowadzi do zmniejszenia wytrzymałości elektrycznej izolacji i jej przebicia.
Metalowa powłoka kabla może ulec zniszczeniu pod wpływem naprężeń mechanicznych, chemicznych lub elektrycznych. środowisko. Szczególnie często powłoki linii kablowych ułożonych w ziemi ulegają zniszczeniu na skutek elektrokorozji wywołanej prądami błądzącymi zelektryfikowanego transportu szynowego, gdzie szyny są wykorzystywane jako przewód powrotny. W przypadku zerwania styku na stykach szyn wzrasta opór czynny torów i część prądu odchodzi do ziemi. Prąd przepływa przez metalowe osłony kabli o niskiej rezystancji do ujemnego bieguna źródła zasilania. Za pomocą pomiarów określa się różnicę potencjałów między powłoką kabla a ziemią, gęstość prądu płynącego z kabla do ziemi, napięcie i prąd płynący przez powłokę. Obszary niebezpieczne to obszary, w których powłoki kabli mają dodatni potencjał względem ziemi lub różnicę potencjałów względem strefy o zerowym potencjale.
Aby chronić kable przed korozją elektryczną, stosuje się ochronę katodową, protektorową i drenaż elektryczny. Ochrona katodowa z wykorzystaniem zewnętrznego źródła prądu stałego tworzy ujemną polaryzację w chronionym metalu (pancerz i metalowa osłona kabla). Ochronę ochronną stosuje się przy małych prądach błądzących w strefie anodowej i przemiennej, w obecności dodatniego potencjału powłoki kabla, nie przekraczającego w stosunku do ziemi 0,3 V. Zabezpieczenie polega na tym, że elektroda (protektor) jest podłączona do osłony kabla składa się z metalu stopowego, który ma wyższy potencjał ujemny niż osłona kabla. Powoduje to krążenie prądu od osłony do elektrody.
Ekranowany metodą odwodnienia elektrycznego polega na zastosowaniu metalowej zworki, która kieruje prądy błądzące z osłon kabli na szyny lub do strefy uziemienia, gdzie nie występują prądy błądzące. W takim przypadku osłony kabli nabierają potencjału ujemnego i proces ich korozji ustaje.
Konserwacja linii lotniczych
Napowietrzna linia elektroenergetyczna jest w trakcie eksploatacji narażona na różne obciążenia. Podpory przenoszą stałe obciążenie od własnej masy drutów, izolatorów, kształtek, a także zmienne obciążenie od wpływu lodu i naporu wiatru. Jednocześnie podpory podlegają procesom starzenia, a drewniane - rozkładowi. Przewody linii napowietrznej narażone są na prądy obciążeniowe, prądy awaryjne, wahania temperatury powietrza, drgania pod wpływem wiatru oraz obciążenia mechaniczne od lodu i śniegu.
W celu zapewnienia niezawodnej i bezawaryjnej pracy linii napowietrznych plany ruchu technicznego przewidują następujące działania:
- inspekcje VL;
- zgodność z dopuszczalnymi trybami pracy linii napowietrznych;
- przeprowadzanie badań i pomiarów prewencyjnych;
- dokonywanie napraw;
- badanie przyczyn wypadków i opracowywanie środków ich eliminacji.
Linie napowietrzne są kontrolowane co najmniej raz w miesiącu przy napięciach do 1000 V i co najmniej raz w roku przy napięciach powyżej 1000 V. Przeglądy okresowe dzielą się na dzień, noc, jazdę i kontrolę.
Podczas przeglądów dziennych sprawdzany jest ogólny stan linii i jej tras oraz identyfikowane są poszczególne usterki. Podczas kontroli zwraca się uwagę na integralność izolatorów, stan podpór i poprawność ich położenia, integralność bandaży i skarp uziemienia, stan połączeń stykowych przewodów, odgałęzień doprowadzeń, kabla zjazdy i zakończenia, warunek środki ochrony kable przed uszkodzeniami mechanicznymi. Sprawdza się brak pęknięć i przetopienia poszczególnych przewodów przewodów, oznaki przegrzania złączy, przewodów na przewodach, które mogą prowadzić do zwarcia faz. Górna część wsporników, druty, izolatory i mocowania są oglądane przez lornetkę. Każde odchylenie podpór od normalnego położenia prowadzi do wzrostu momentu zginającego, zmniejszenia nośności podpory, co może prowadzić do jej uszkodzenia. Podczas inspekcji trasy BJ1 zwraca się uwagę na wysokość i częstotliwość występowania zarośli na trasie, obecność pojedynczych drzew grożących upadkiem na druty. Podczas oględzin bandaże są napinane, a numeracja podpór zostaje przywrócona.
Podczas wykonywania inspekcji liniowych liniowy nie może wspinać się na podpory. Linia w każdym przypadku jest uważana za pod napięciem.
Głównym celem nocnych przeglądów linii napowietrznych jest identyfikacja wyładowań iskrzących lub żarzenia na skutek nagrzewania się styków w niezadowalającym stanie styków. Inspekcja przeprowadzana jest w deszczową pogodę.
Po zakończeniu przeglądów dziennych i nocnych wypełniana jest karta kontroli z zapisem zaobserwowanych w niej usterek. Jeśli awarie mogą prowadzić do awaryjnego uruchomienia linii napowietrznej, są one natychmiast eliminowane.
Podczas oględzin z ziemi nie jest możliwe wykrycie wszystkich wad linii napowietrznej. Dlatego plany Konserwacja przewidzieć przeglądy konne linii napowietrznych co najmniej 1 raz na 3 lata przy odłączonym napięciu z linii. Podczas kontroli jazdy sprawdzany jest stan górnych części podpór, określany jest stopień ich zaniku, stan izolatorów, haków, cięgien, wtyczek, połączeń i naprężeń przewodów, niezawodność mocowania ograniczników rurowych, zakończeń kablowych są oceniane. Podczas tych prac wymieniane są uszkodzone izolatory, haki, tablice ostrzegawcze, napinane są zwisające przewody, odrdzewiane, a wszystkie miejsca łączenia skarp uziemiających są pokrywane smarem antykorozyjnym. Sprawdzenie drewna pod kątem próchnicy przeprowadza się raz na 3 lata i łączy się z inspekcją jeździecką. Głębokość zaniku jest określana jako średnia arytmetyczna z kilku pomiarów. Podpora lub mocowanie są uważane za nieodpowiednie do dalszego użytku, jeśli głębokość rozpadu wzdłuż promienia kłody jest większa niż 3 cm przy średnicy kłody 25 cm lub większej.
Kontrolę stanu zamocowań żelbetowych z selektywnym otwieraniem gruntu przeprowadza się raz na 6 lat, począwszy od czwartego roku eksploatacji. Sprawdza się brak pęknięć poprzecznych lub ukośnych, miejsc odsłonięcia zbrojenia metalowego, odprysków betonu itp.
Z biegiem czasu z powodu nietrwałości oporność gleba, obecność wilgoci w glebie, zmienia się rezystancja urządzeń uziemiających, więc są one również sprawdzane.
ROSYJSKA SPÓŁKA AKCYJNA "ROSKOMMUNENERGO" ZALECENIA METODYCZNE DOTYCZĄCE KONSERWACJI I NAPRAW SPRZĘTU I OBIEKTÓW LINIOWYCH PUBLICZNYCH SIECI ELEKTRYCZNYCH WYDANIE 1 Konserwacja i naprawa stacji transformatorowych 6-10/0,4 kV ZatwierdzonyGlavgosenergonadzor Rosji(pismo nr 42-04-05/352 z 14.08.96) Energoatomizdat
Moskwa 1996Spis treści
1. Wprowadzenie 2. Postanowienia ogólne dotyczące organizacji eksploatacji TP 3. Planowanie przeglądów i napraw TP 4. Utrzymanie ruchu TP 5. Ocena stanu technicznego TP 6. Przeprowadzanie napraw TP 7. prowadzenie dokumentacji technicznej do obsługi i napraw TP Załącznik nr 1 Wykaz regulaminu DOKUMENTACJI TECHNICZNEJ WYKORZYSTYWANEJ W EKSPLOATACJI TP ZAŁĄCZNIK 2 SERWIS TP, RP 6-10/0,4 kV ZAŁĄCZNIK 3 ROCZNY HARMONOGRAM KONSERWACJI I NAPRAW TS, RP 6-10/0,4 kV ZAŁĄCZNIK 4 HARMONOGRAM ODŁĄCZANIA TS 6-10 kV ZAŁĄCZNIK 5 SPRAWOZDANIE Z KONSERWACJI I NAPRAW Stacja transformatorowa 6-10/0,4 kV ZAŁĄCZNIK 6 PRACE REMONTOWE w stacji transformatorowej 6-10/0,4 kV ZAŁĄCZNIK 7 WYKAZ USTEREK TC ZAŁĄCZNIK 8 USTAWA SPRAWOZDANIE Z NAPRAWY TC ZAŁĄCZNIK 9 WYKAZ DOKUMENTACJI TECHNICZNEJ TC W PRACY ZAŁĄCZNIK 10 PASZPORT UŻYTKOWANIA TP ZAŁĄCZNIK 11 KARTA TYPOWA SCHEMAT ELEKTRYCZNY TP (PRZYKŁAD NAPEŁNIANIA PTS 10/0,4 kV, 25 kVA) DODATEK 12 KARTA KONTROLI TP 6-10/0,4 kV TP TS 6-10/0,4 kV DODATEK 14 DZIENNIK REJESTRACJI WYNIKÓW BADAŃ SPRZĘTU TS 6-10 /0,4 kV ZAŁĄCZNIK 15 REJESTR USTEREK TS 6-10/0,4 kV |
1. WSTĘP
Terminowa konserwacja i naprawa urządzeń i konstrukcji liniowych jest jednym z elementów systemu prewencyjnego utrzymania ruchu (PPR), który zapewnia niezawodne funkcjonowanie rozdzielczych sieci elektrycznych. Podczas konserwacji i napraw należy stosować system kontroli jakości, aby zapewnić wykonywanie prac zgodnie z wymaganiami dokumentów regulacyjnych i technicznych, których wykaz znajduje się w Załączniku 1 do niniejszych Wytycznych. Prace należy wykonywać zgodnie z wymogami przepisów bezpieczeństwa i przeciwpożarowych. Zalecenia metodyczne określają procedurę przeprowadzania środków organizacyjnych i technicznych w zakresie konserwacji i naprawy podstacji transformatorowych 6-10 / 0,4 kV. Na ich podstawie można sporządzić lokalne instrukcje w przedsiębiorstwach użyteczności publicznej (przedsiębiorstwach elektroenergetycznych), uwzględniające specyficzne warunki pracy i stosowane metody pracy. W tekście Wytycznych stosowane są następujące terminy, ich definicje i skróty.
Terminy, skróty |
Definicje |
TP | Stacje transformatorowe typu MTP, KTP, KTPP, ZTP o napięciu 6-10/0,4 kV oraz punkty rozdzielcze 6-10 kV | Dokumentacja normatywno-techniczna dla TP | Aktualna dokumentacja dyrektywy do projektowania, budowy i eksploatacji TP, dokumentacja techniczna dla TP | Wada elementu TC | Niezgodność elementu TP z wymaganiami określonymi w dokumentacji regulacyjno-technicznej, która nie prowadzi do natychmiastowego automatycznego wyłączenia TP lub jego części | Uszkodzenie elementu (części) TP | Zdarzenie polegające na całkowitej utracie stanu eksploatacyjnego elementu (części) TS i prowadzące do natychmiastowego automatycznego wyłączenia TS lub jego części, zniszczenia tego elementu lub części TS | Stan techniczny TP | Ocena jakościowa lub ilościowa, wyznaczana przez sumę wad elementów, części procesu technologicznego, zarejestrowanych podczas procesu utrzymania ruchu | PES | Przedsiębiorstwo sieci elektrycznych | OZE | Dzielnica sieci elektrycznych (jednostka strukturalna PSZ) |
2. POSTANOWIENIA OGÓLNE O ORGANIZACJI DZIAŁANIA TP
2.1. Główne rodzaje prac operacyjnych wykonywanych w TP to konserwacja i naprawa. 2.2. Konserwacja składa się z zestawu środków mających na celu ochronę TC, ich elementów i części przed przedwczesnym zużyciem. 2.3. Naprawa SP, ich elementów i części polega na przeprowadzeniu szeregu działań mających na celu utrzymanie lub przywrócenie pierwotnej sprawności i parametrów SP, ich elementów i części. Podczas napraw zużyte (wadliwe) elementy i wyposażenie wymieniane są na równorzędne lub bardziej zaawansowane pod względem ich właściwości. 2.4. Podczas konserwacji i napraw usterki i uszkodzenia są identyfikowane i eliminowane w zaplanowany sposób. Wady i uszkodzenia TS, ich elementów i części, które bezpośrednio zagrażają bezpieczeństwu ludności i personelu konserwacyjnego poprzez wystąpienie pożaru, muszą być natychmiast usunięte. 2.5. Konserwacja i naprawa podstacji transformatorowych z reguły powinna być połączona z podobnymi pracami na wychodzących liniach przesyłowych 0,38 kV. 2.6. W PES (OZE) do wykonywania remontów podstacji transformatorowych zaleca się tworzenie wyspecjalizowanych jednostek do naprawy części konstrukcyjnej podstacji transformatorowej, do naprawy wyposażenia podstacji transformatorowych zgodnie z RDTP 34-38-046- 87 „Industrializacja remontu urządzeń dla sieci rozdzielczych 0,38-20 kV” oraz do badań. 2.7. Zespoły zajmujące się scentralizowaną konserwacją i naprawą TP muszą być wyposażone w mechanizmy, pojazdy, urządzenia olinowania, narzędzia, sprzęt ochronny, sprzęt komunikacyjny, dokumentację techniczną, produkcję, opisy stanowisk i instrukcje bezpiecznej pracy. 2.8. Niedozwolone jest dokonywanie zmian w konstrukcji podstacji transformatorowych i związanych z nimi urządzeń, które zmniejszają wydajność. : Uzasadnione technicznie zmiany w projekcie TP, które nie wpływają na obniżenie wydajności eksploatacyjnej, mogą być przeprowadzone decyzją głównego inżyniera TPP. 2.9. Podczas eksploatacji podstacji transformatorowej wszelkie prace niezbędne do konserwacji, naprawy i przebudowy muszą być wykonywane w strefach bezpieczeństwa regulowanych „Zasadami ochrony sieci elektrycznych”.3. PLANOWANIE KONSERWACJI I NAPRAW TP
3.1. Jako przedmiot planowania konserwacji i naprawy z reguły należy wziąć TP lub kilka TP w jednym kierunku (podajnik). 3.2. Aby zapewnić planowanie prac związanych z konserwacją i naprawą TP, zaleca się sporządzenie: 3.2.1. Wieloletni (przez 6 lat) harmonogram konserwacji (Załącznik 2); 3.2.2. Roczny harmonogram obsługi technicznej i napraw TP (Załącznik 3); 3.2.3. Plan-harmonogram wyłączeń TS na miesiąc (Załącznik 4); 3.2.4. Miesięczny raport z konserwacji i napraw TP (Załącznik 5). 3.3. Zgodnie z niniejszymi Wytycznymi sporządzane są wieloletnie i roczne harmonogramy konserwacji. Wskazane harmonogramy powinny być skoordynowane z harmonogramami utrzymania linii 0,38 kV wychodzących ze stacji transformatorowej. 3.4. Roczny harmonogram remontów HP opracowywany jest na podstawie wieloletniego harmonogramu i oceny stanu technicznego HP z uwzględnieniem kategorii odbiorców, planów odbudowy, warunków eksploatacji, dostępności siły roboczej, zasobów materialnych i finansowych. Harmonogram musi koniecznie przewidywać naprawy obiektów systemów podtrzymywania życia miast i miasteczek (zaopatrzenie w ciepło, zaopatrzenie w wodę itp.). 3.5. Zalecana częstotliwość napraw TP to co najmniej raz na 6 lat. 3.6. Co roku zaleca się sporządzenie dwóch rocznych harmonogramów napraw dla TS: jeden dla TS, którego naprawa jest konieczna w planowanym roku, drugi dla TS, którego naprawa planowana jest w roku następującym po planowanym (skorygowana w przyszłym roku). 3.7. Dla TS, których naprawa planowana jest w planowanym roku, na podstawie kart kontrolnych i rejestru usterek sporządzane są zestawienia prac naprawczych (załącznik 6). Wykaz prac naprawczych powinien również uwzględniać średnią ilość napraw nadzwyczajnych TS, które ulegają nienormalnej awarii. 3.8. Zgodnie z arkuszami napraw TP przeprowadzane są obliczenia zasobów materiałowych i kosztów pracy, potrzeby transportu i specjalnych mechanizmów, a także opracowywane są szacunki i specyfikacje dotyczące obiektów naprawczych określonych w harmonogramie. 3.9. W przypadku TS, którego naprawa planowana jest w roku następującym po planowanym, sporządzane są zestawienia dotyczące niezbędnego sprzętu i materiałów. 3.10. Miesięczny harmonogram wyłączania SP opracowywany jest na podstawie rocznego harmonogramu remontów SPW (dla SP zlokalizowanych na terenach wiejskich uwzględnia się sezonowość prac rolniczych) i w miarę możliwości uzgadniany z odbiorcami zaplanowanymi na zamknąć. 3.11. Zaleca się, aby prace nad testowaniem wyposażenia elektrycznego podstacji transformatorowej zaplanować w terminie pokrywającym się z naprawą odpowiedniej podstacji transformatorowej. Testowanie sprzętu elektrycznego może być przeprowadzane wyłącznie przez laboratoria certyfikowane i zarejestrowane w sposób ustalony przez Glavgosenergonadzor Rosji (list informacyjny z dnia 22.01.91 nr 94-6 / 3-ET).4. KONSERWACJA TECHNICZNA
4.1. Utrzymanie TP obejmuje prace wymienione w tabeli. jeden. Tabela 1. Wykaz prac konserwacyjnych dla TP
Nazwa prac |
Częstotliwość trzymania |
Notatka |
regularne inspekcje |
1. Inspekcja podstacji transformatorowej przez elektryków | Raz w roku | Wypełnij arkusz kontrolny | 2. Kontrola przez personel inżynieryjno-techniczny wybranej liczby TS | Raz w roku | Wypełnij arkusz kontrolny | 3. Inspekcja SP ujęta w rocznym harmonogramie napraw przez personel inżynieryjno-techniczny | W ciągu roku poprzedzającego rok remontu stacji transformatorowej | Nadzwyczajne inspekcje | 4. Inspekcja po zjawiskach przyrodniczych (badane są wszystkie TS znajdujące się w strefie zjawisk przyrodniczych) | Pod koniec naprawy nadzwyczajnej lub następnego dnia | Wypełnij arkusz kontrolny | 5. Kontrola TP po każdym przypadku: | działanie wyłączników TP w celu wyłączenia zwarcia (załączenie na zwarcie) | Kiedy przyczyna i skutek zostaną wyeliminowane lub następnego dnia | Wypełnij arkusz kontrolny | przepalone bezpieczniki | Podczas wymiany wkładki bezpiecznikowej | 6. Inspekcja kluczowych obiektów (VIE) | Przed rozpoczęciem sezonu grzewczego Kontrole | Na podstawie wyników kontroli sporządzana jest lista napraw. | 7. Sprawdzenie części konstrukcyjnej TP | W trakcie kontroli (poz. 3) | Wypełnij arkusz kontrolny | 8. Sprawdzenie integralności uziemienia podstacji transformatorowej | Także | Także | pomiary | 9. Pomiary obciążenia prądowego na wejściach transformatora 0,4 kV i linii odpływowych | 2 razy w roku (w okresach minimalnych i maksymalnych obciążeń) | Arkusze pomiarowe są wypełnione | 10. Pomiar napięcia szyny 0,4 kV | Kompatybilny z pomiarami obciążenia | Także | 11. Pomiar poziomu prądu zwarciowego lub rezystancji obwodu „zero fazowego” linii odpływowych 0,4 kV | W razie potrzeby, ale przynajmniej raz na 6 lat | Także | Testy, pomiary | 12. Pomiar rezystancji izolacji rozdzielnicy 6-20 kV i 0,4 kV | Podczas remontu TP, ale co najmniej 1 raz na 6 lat | Dziennik testów sprzętu TP jest wypełniany | 13. Pomiar rezystancji ograniczników zaworów | Także | Także | 14. Pomiar prądu przewodzenia ograniczników zaworów | Także | Także | 15. Pomiar rezystancji uziemienia lub napięcia dotykowego do powłok i uziemionych elementów | Podczas remontu TP raz na 6 lat | Dziennik testów sprzętu TP jest wypełniany | 16. Pomiar rezystancji izolacji uzwojeń transformatorów mocy | 1 raz na 3 lata | Także | 17. Badanie urządzeń i izolacji 6-10 kV podwyższonym napięciem o częstotliwości przemysłowej 50 Hz | 1 raz na 6 lat 1 raz na 6 lat | Takie samo | 18. Badanie oleju transformatorowego transformatorów mocy o mocy powyżej 630 kVA | Także | Podobnie | 19. Sprawdzanie zabezpieczenia przekaźnika | 1 raz na 3 lata | Także | Prace indywidualne | 20. Czyszczenie izolacji urządzeń, urządzeń, zbiorników i armatury TP z kurzu i brudu | W razie potrzeby | 21. Czyszczenie, smarowanie i dokręcanie połączeń stykowych | Także | 22. Eliminacja niewspółosiowości mechanizmów napędowych i części stykowej wyłączników i odłączników (odbiorników) | Także | 23. Konserwacja transformatora | 1 raz na 3 lata | 24. Smarowanie przegubów i powierzchni trących urządzeń | W razie potrzeby | 25. Dodanie świeżego oleju do aparatury i sprzętu wypełnionego olejem, zastąpienie żelu krzemionkowego | Podobnie | 26. Aktualizacja i wymiana napisów dyspozytorskich, schematów mnemonicznych, tablic ostrzegawczych i znaków bezpieczeństwa w rozdzielni 0,4-10 kV | Podobnie | 27. Wymiana wkładek bezpiecznikowych | Przy zmianie trybów pracy sieci i parametrów chronionego sprzętu, gdy przepalą się bezpieczniki | 28. Cięcie krzewów w strefie chronionej TP, przycinanie | W razie potrzeby | 29. Przywrócenie martwego obszaru podstawy TP | Także | 30. Remont dachu podstacji transformatorowej | Podobnie |
5. OCENA STANU TECHNICZNEGO TP
5.1. Ocena stanu technicznego stacji transformatorowej powinna być zorganizowana i przeprowadzona w PES (OZE) zgodnie z „Instrukcją rozliczania i analizy w systemach elektroenergetycznych stanu technicznego sieci rozdzielczych o napięciu 0,38-20 kV z linie lotnicze przesył energii” (M.: SPO Soyuztekhenergo, 1990), „Wytyczne dotyczące kompleksowej oceny jakościowej stanu technicznego sieci rozdzielczych o napięciu 0,38-20 kV wraz z napowietrznymi liniami energetycznymi”. RD 34.20.583-91 (M. : SPO ORGRES, 1993) oraz niniejszych Wytycznych 5.2 Przy ocenie stanu technicznego ST zaleca się ich reprezentowanie przez następujące jednostki naprawy warunkowej (URE): - jednotransformatorowe TS (MTP, KTP, ZTP); sekcja jednotransformatorowa w ramach wielotransformatorowej TS (KTP, ZTP) - sekcja (szafa) punktu rozdzielczego 10 kV z elementów rozdzielnicy (KRUN) 5.3 Wskaźniki oceny stanu technicznego stacji transformatorowej , stan podstacji transformatorowej, składającej się z kilku URE, należy określić jako sumę odpowiednich wskaźników dla tych URE, ich elementy: - obudowa szafy, komory, przedziału, - główne wyposażenie. szafy, komory i przegródki yat jako obudowy rozdzielni 6-20 kV KPT, a dla urządzeń głównych - jak dla transformatora mocy KTP. Dla tych elementów URE należy zastosować odpowiednie wartości współczynników ważenia. 5.4. Kadra inżynieryjno-techniczna PSZ (OZE) powinna corocznie określić stan techniczny każdej SP i ustalić planowany termin ich naprawy, a dla SP zaplanowanej do naprawy w planowanym roku określić ilość prac remontowych do sporządzić listę napraw.6. WYKONYWANIE NAPRAW TP
6.1. Przed przekazaniem podstacji transformatorowej do naprawy wszystkie niezbędne Praca przygotowawcza oraz koordynacja z zainteresowanymi służbami PSZ i stronami trzecimi. 6.2. Przed rozpoczęciem naprawy podstacja transformatorowa musi zostać dostarczona niezbędne materiały, sprzęt i mechanizmy specjalne. Wszyscy uczestnicy prac remontowych na obiekcie muszą zapoznać się z charakterem i zakresem nadchodzących prac oraz warunkami ich realizacji nie później niż z jednodniowym wyprzedzeniem. 6.3. Podczas napraw SPW mogą być wykonywane następujące prace: 6.3.1. Demontaż i wymiana uszkodzonych elementów odłączników, rozłączników i ich napędów, drążków do napędów odłączników, urządzeń blokujących, urządzeń kompensacji mocy biernej. 6.3.2. Demontaż i wymiana uszkodzonych biegunów wyłączników olejowych i próżniowych, odgromników, bezpieczników, przekładników, wyłączników niskonapięciowych. 6.3.3. Demontaż i wymiana uszkodzonych (przeciążonych) transformatorów mocy. 6.3.4. Demontaż i wymiana przewodów 0,4 kV wewnątrz i na zewnątrz podstacji transformatorowej. 6.3.5. Demontaż i wymiana uszkodzonej izolacji wejść, izolacja szyn zbiorczych 0,4-10 kV, naprawa puszek kablowych. 6.3.6. Wymiana i naprawa łączności, zabezpieczenia przekaźników i automatyki. 6.3.7. Remonty budynków - ściany, podłogi, studzienki kablowe, stropy, drzwi, dachy, fundamenty. 6.3.8. Wymiana i naprawa stojaków, przystawek, łóżek, trawersów, bandaży, punktów mocowania i przegubów, podestów, poręczy, schodów, wsporników MTP i KTP. 6.3.9. Naprawa urządzeń uziemiających, odbudowa i wzmocnienie pętli uziemienia i przewodów uziemiających. 6.3.10. Prace konserwacyjne, w zakresie terminów zbiegających się z remontem stacji transformatorowej. 6.4. Naprawa TS powinna być przeprowadzona zgodnie z mapami technologicznymi i, jeśli to konieczne, zgodnie z projektami organizacji prac naprawczych. 6.5. Prace naprawcze po zakończeniu są akceptowane i oceniane zgodnie z jakością wykonania. Ocenę jakości pracy musi przeprowadzić komisja powołana na zlecenie dla PES (OZE), z przygotowaniem aktu-raportu o naprawie (Załącznik 8). 6.6. Naprawę uważa się za zakończoną, jeżeli wykonane zostały wszystkie prace przewidziane w wykazie napraw TP. Zatwierdzony raport naprawy jest podstawą do odzwierciedlenia kosztów i odpisania materiałów, urządzeń, paliw i smarów.7. KONSERWACJA DOKUMENTACJI TECHNICZNEJ DLA KONSERWACJI I NAPRAW TP
7.1. PSZ (OZE) muszą utrzymywać dokumentację techniczną wskazaną w tabeli. 2. Tabela 2. Lista zalecanej dokumentacji technicznej do eksploatacji TP
Okres trwałości |
1. Dokumentacja do przyjęcia procesu technologicznego do eksploatacji | 2. Paszport operacyjny | Także | 3. Arkusz kontroli TP | Do następnego remontu | 4. Arkusz do pomiaru obciążeń i napięć TP | 5 lat | 5. Dziennik wad TC | Przez cały okres funkcjonowania TP | 6. Dziennik rejestracji wyników testów sprzętu | Także |
ZAŁĄCZNIK 1
WYKAZ DOKUMENTACJI REGULACYJNEJ I TECHNICZNEJ WYKORZYSTYWANEJ W DZIAŁANIU TP
1. Zasady montażu instalacji elektrycznych. M.: Energoatomizdat, 1986. 2. Zasady eksploatacji technicznej elektrowni i sieci. M.: Energoatomizdat, 1989. 3. Zbiór materiałów dyrektywnych Głównego Wydziału Technicznego Ministerstwa Energii ZSRR (część elektrotechniczna). Moskwa: Energoatomizdat, 1985. 4. Normy testowania urządzeń elektrycznych. M.: Atomizdat, 1978. 5. Zasady ochrony sieci elektrycznych o napięciach powyżej 1000 V. M.: Energoatomizdat, 1985. 6. Zasady ochrony sieci elektrycznych o napięciach do 1000 V. M.: Energoizdat, 1973. 7. Zasady bezpieczeństwa do obsługi instalacji elektrycznych. M.: Energoatomizdat, 1987. 8. Zasady eksploatacji konsumenckich instalacji elektrycznych. M.: Energoatomizdat, 1992. 9. Zasady bezpieczeństwa eksploatacji instalacji elektrycznych użytkowych. M.: Energoservis, 1994. 10. Zbiór zasad i instrukcji stosowanych w eksploatacji konsumenckich instalacji elektrycznych. M.: Energoservis, 1995. 11. Zbiór zasad i instrukcji stosowanych w eksploatacji konsumenckich instalacji elektrycznych. Część 11 ”. M .: Energoservice, 1995. 12. Zasady użytkowania i testowania sprzętu ochronnego stosowanego w instalacjach elektrycznych. Wymagania techniczne dla nich (wydanie 9). M .: Energoatomizdat, 1993. 13. Normy czasowe naprawy i konserwacja linii lotniczych i kablowych, podstacji transformatorowych i punktów dystrybucji 0,4-20 kV, M.: SPO Soyuztekhenergo, 1985. 14. Typowe normy czasu na remonty i konserwację sieci elektrycznych, urządzeń i wyposażenia elektroenergetycznego, M.: TsNIIS , 1990. 15. Departamentalne powiększone ceny jednostkowe za naprawę i konserwację sieci elektrycznych przedsiębiorstw energetycznych Ministerstwa Energii ZSRR. Wydanie 2. M.: SPO Soyuztekhenergo, 1988. 38-10 kV Gosplan KazSSR, 1985. 17. Fabryka instrukcja obsługi urządzeń elektrycznych stosowanych w podstacjach transformatorowych 6-10/0,4 kV i punkty dystrybucyjne 6-20 kV. 18. Wskaźniki zużycia materiałów i wyrobów do naprawy i konserwacji kompletnych stacji transformatorowych o napięciu 10/0,4 kV oraz masztowych stacji transformatorowych o napięciu 6-20/0,4 kV. M.: SPO Soyuztekhenergo, 1985. 19. Normy ubezpieczenia awaryjnego części zamiennych do masztów i kompletnych podstacji transformatorowych 6-20 / 0,38 kV. M.: Soyuztekhenergo, 1986. 20. Wytyczne dotyczące określenia zapotrzebowania na mechanizmy działania i naprawy komunalnych sieci elektrycznych i cieplnych. M .: 1996. 21. Wytyczne dotyczące regulacji i konserwacji wyłączników serii AB 2000, A 3100. M .: SPO ORGRES, 1991. 22. Wytyczne dotyczące regulacji i konserwacji wyłączników serii A 3700. M .: SPO Soyuztekhenergo, 1981. 23. Wytyczne dotyczące regulacji i działania wyłączników serii ABM. M .: SPO Soyuztekhenergo, 1978. 24. Metodyczne. instrukcję obsługi wyłączników serii AP 50. M.: SPO ORGRES, 1975. 25. Zalecenia dotyczące sposobu konserwacji automatycznych wyłączników połączeń 0,4 kV oraz środków zabezpieczenia przekaźnikowego połączeń 6/35 kV przy użyciu kompletnych urządzenia serii SATURN. M.: SPO ORGRES, 1994. 26. Wytyczne obliczania prądów zwarciowych w sieci o napięciu do 1 kV elektrowni i stacji elektroenergetycznych z uwzględnieniem wpływu łuku elektrycznego. M.: SPO ORGRES, 1993. 27. Wskaźniki zużycia materiałów i wyrobów do napraw remontowych i bieżących kompletnych stacji transformatorowych o napięciu 10/0,4 kV i masztowych stacji transformatorowych o napięciu 6-20/0,4 kV. HP-34-70-80-85. Soyuztekhenergo, 1985. 28. Zasady bezpieczeństwa przeciwpożarowego dla przedsiębiorstw energetycznych. DR 34.03.301-87 (PPB 139-87). Energoatomizdat, 1988. 29. Typowa instrukcja ochrony pracy dla elektryka przy konserwacji podstacji. DR 34.03.121-87. Sojuztekhenergo, 1988.ZAŁĄCZNIK 2
WIELOLETNI HARMONOGRAM KONSERWACJI TS, RP 6-10/0,4 kV
PES dla OZE„Zatwierdź” główny inżynier
Czas (lata) |
Nazwa prac |
Nazwa obiektu |
Zakres prac (objętość fizyczna / plan) |
19____ | 19____ | 19____ |
DODATEK 3
ROCZNY HARMONOGRAM KONSERWACJI I NAPRAW TS, RP 6-10/0,4 kV
PES dla OZE przez rok "Zatwierdź" Główny Inżynier Szef RESAgreed (PTO PES)DODATEK 4
Uzgodnione Zatwierdzone przez głównego inżyniera PESPLAN-HARMONOGRAM ODŁĄCZENIA TS 6-10 kV
zgodnie z ____________ OZE dla _____________ 19___ (miesiąc)
Nazwa obiektu numer TP, rodzaj pracy |
Notatka |
Trwanie |
Trwanie |
DODATEK 5
RAPORT Z KONSERWACJI I NAPRAW TS 6-10/0,4 kV
PES____ RES______________ dla _________ miesiąc, rok
Nazwa prac |
jednostka. obrót silnika. |
Plan na rok |
Ukończone od początku roku |
Plan kamei. |
Gotowe. na miesiąc |
Dokument potwierdzający |
DODATEK 6
SPRAWOZDANIE Z PRAC REMONTOWYCH W STACJI TRANSFORMATOROWEJ 6-10/0,4 kV
Nazwa przedmiotu, numer TP, typ |
Kod rozliczenia |
Numer listy |
Numer arkusza |
Nazwa (kod) pracy |
wymiana transformatora mocy, |
wymiana przełącznika |
wymiana odłącznika |
URUCHOM wymianę |
wymiana ogranicznika |
wymiana izolatora |
DODATEK 7
LISTA WAD TC
1. część budowlana 1.1. Drewniany stojak: gnicie; Pękanie; palenie; złamanie 1.2. Przedrostek drewniany: gnicie; Pękanie; palenie; złamanie 1.3. Trawersy drewniane, belki poprzeczne: gnicie; pękanie 1.4. Bandaż: osłabienie; korozja 1.5. Poluzowanie krawata trawersu ze stojakiem 1.6. Uszkodzenie skarpy uziemiającej 1.7. Mocowanie żelbetowe: odsłonięcie zbrojenia, pękanie; złamanie 1.8. Ugięcie drewnianego stojaka ponad dopuszczalne wartości 1,9. Ugięcie stelaża żelbetowego ponad wartości dopuszczalne, 1.10. Słupek żelbetowy: pękanie; nachylenie przekraczające dopuszczalne wartości; przerwa 1.11. Uszkodzenie obejmy, mocowanie amortyzatora 1.12. Uszkodzenie pałąka 1.13. Trawers metalowy: korozja; zniszczenie; ugięcie 1.14. Rama nośna: gnijąca; pękanie 1.15. Korozja ramienia napędu odłącznika 1.16. Korozja wspornika iskiernika 1.17. Poprzeczka: gnicie; pękanie 1.18. Korozja ciągu napędu odłącznika 1.19. Uszkodzenie ramienia napędu odłącznika 1.20. Uszkodzenie wspornika iskiernika 1.21. Uszkodzenie ciągu napędu odłącznika 1.22. Odłącz ramkę: przekrzywić; korozja; uszkodzenia 1.23. Obszary obsługi: uszkodzenia; korozja 1.24. Stelaż fundamentowy, łóżko: zniszczenie; ekspozycja zbrojenia; pękanie 1.25. Uszkodzenie ramy nośnej KTP, KRUN 1.26. Pętla uziemienia: uszkodzenie; odporność powyżej normy 1.27. Uszkodzenie urządzeń blokujących 1.28. drzwi TP: uszkodzenie; korozja 1.29. Szafy, skrzynki KRUN: uszkodzenia zewnętrzne: korozja 1.30. Uszkodzenie fundamentu TP 1.31. Uszkodzenia uszczelnień, hydroizolacja fundamentów 1.32. Uszkodzenie paneli ściennych 1.33. Uszkodzenie dachu budynku TP 1.34. Uszkodzenia dołów, kanałów kablowych TP 1.35. Uszkodzenie podłogi TP 1.36. Korozja zatopionych części budynku TP 1.37. Brak numeracji, oznaczeń wysyłkowych, plakatów ostrzegawczych 1.38. Korozja obudowy ochronnej, skrzynki, siatki ochronnej 1.39. Uszkodzenie obudowy ochronnej, skrzynki, siatki siatkowej 1.40. Uszkodzenia wsporników, pinów urządzeń wyjściowych 1.41. Uszkodzenie zbiornika oleju 1.42. Uszkodzenie oświetlenia TP, RP 1.43. Uszkodzenie ogrodzenia 1.44. Uszkodzenie martwego obszaru 1.45. Zaśmiecanie strefy bezpieczeństwa 1.46. Uszkodzenie sprzętu przeciwpożarowego 1.47. Brakujące lub uszkodzone wyposażenie ochronne 2. RU 6-10KV 2.1. Brak numeracji, oznaczenia dyspozytorskie 2.2. Brak oznaczenia kolorystycznego opon 2.3. Rzuć obecność ciał obcych w częściach przewodzących prąd. 2.4. Izolatory kołków: wyszczerbione; zanieczyszczenie; zniszczenie 2.5. Tuleje: wyszczerbione; zanieczyszczenie; zniszczenie 2.6. Izolatory wsporcze: rozdrobnione; zanieczyszczenie; zniszczenie 2.7. Izolatory przepustów kablowych: wyszczerbione; zanieczyszczenie; zniszczenie 2.8. Uszkodzenie uszczelki tulei 2.9. Uszkodzenie obudowy przepustu kablowego 2.10. Uszkodzenie styków odłącznika, przełącznika obciążenia 2.11. Uszkodzenie styków zamka bezpieczeństwa 2.12. Uszkodzenie osłony wkładki topikowej zamka bezpieczeństwa 2.13. Dostępność niestandardowej wkładki bezpiecznikowej 2.14. Uszkodzenie drążka napędowego odłącznika, wyłącznik obciążenia 2.15. Zwiększone nagrzewanie skręcanych połączeń szynoprzewodów 2.16. Uszkodzenie szyny zbiorczej 2.17. Uszkodzenie przekładnika prądowego 2.18. Uszkodzenie przekładnika napięciowego 2.19. Uszkodzenie napędu łamacza 2.20. Uszkodzenie bieguna wyłącznika 2.21. Uszkodzenie blokady odłącznika, wyłącznik obciążenia 2.22. Uszkodzenie blokady wyłącznika (olej, podciśnienie) 2.23. Uszkodzenie ogranicznika zaworu 2.24. Wyciek oleju z wyłącznika napełnionego olejem 2.25. Wyciek oleju z przekładnika napięciowego 2.26. Obniżenie oleju w aparacie wypełnionym olejem 2.27. Uszkodzenie urządzenia RPA 2.28. Uszkodzenie nagrzewnicy aparatu 2.29. Uszkodzenie urządzenia kompensacyjnego3. Transformator mocy 6-10 kV 3.1. Uszkodzenie wejścia 6-10 kV 3.2. Wyciek oleju 3.3. Uszkodzenie obudowy transformatora 3.4. Zwiększony hałas transformatora 3.5. Uszkodzenie wejścia 0,4-0,23 kV 3.6. Uszkodzenie urządzenia do regulacji napięcia 3.7. Uszkodzenie termometru 3.8. Uszkodzenie zbiornika ekspandera 3.9. Zanieczyszczenie obudowy transformatora 3.10. Zanieczyszczenie wejściowe 0,23-10 kV 3.11. Uszkodzenie części nośnej transformatora 3.12. Uszkodzenie wskaźnika poziomu oleju 3.13. Uszkodzenie styku wejściowego 0,4-10 kV 3.14. Przerwanie łańcucha uziemienia obudowy 3.15. Przerwa (odłączenie) szyny neutralnej 3.16. Zmiana koloru żelu krzemionkowego 3.17. Uszkodzenie urządzenia sterującego obciążeniem 3.18. Długotrwałe obciążenie przekraczające dopuszczalne 3.19. Niewystarczający poziom oleju 4. Rozdzielnica 0,4 kV 4.1. Brak numeracji, oznaczenia dyspozytorskie 4.2. Brak oznaczenia kolorystycznego opon 4.3. Rzut, obecność ciał obcych na częściach przewodzących prąd 4.4. Układ odniesienia, izolator przepustowy (tuleja) 4.5. Zanieczyszczenie wzorcowego izolatora przepustowego 4.6. Zniszczenie wzorcowego izolatora przepustowego 4.7. Zniszczenie powłoki izolowanego drutu 4.8. Uszkodzenie styków przełącznika nożowego 4.9. Uszkodzone styki bezpiecznika 4. 10. Uszkodzenie osłony bezpiecznika 4.11. Dostępność niestandardowej wkładki bezpiecznikowej 4.12. Uszkodzenie rękojeści, pchnięcie wyłącznika nożowego (przełącznika) 4.13. Podwyższone nagrzewanie połączeń śrubowych opon 4.14. Uszkodzenie opon 4.15. Uszkodzenie przekładnika prądowego 4.16. Uszkodzenie wyłącznika 4.17. Uszkodzenie ogranicznika 4.18. Zanieczyszczenie izolacji ogranicznika 4.19. Uszkodzenie licznika energii elektrycznej 4.20. Uszkodzenie urządzenia automatyki (ATS, AR itp.) 4.21. Uszkodzenie kondensatora 4.22. Uszkodzenie baterii kondensatorów 4.23. Uszkodzone urządzenie przełączające światła uliczne 4.24. Uszkodzenie urządzeń grzewczych sprzętu 4.25. Uszkodzenie dławika kablowego wlotu kablowegoDODATEK 8
(Przód) AkceptujęGłówny inżynier
ACT-SPRAWOZDANIE Z NAPRAWY TP
________________________________________________________________________________ (nazwa i numer TP) Komisja w składzie ___________________________________________________________ ________________________________________________________________________________ __________________________________________________________________ sporządziła niniejszą ustawę stwierdzając, że ___________________________________________ 19 _____, brygada _____________ wykonała następujące prace remontowe ___________________________________________________________________________ (nazwa i numer TP)
Nazwa prac |
jednostka miary |
Ilość |
Charakterystyka urządzeń elektrycznych |
Nazwa sprzętu i materiałów |
jednostka miary |
Ilość |
Notatka |
DODATEK 9
WYKAZ DOKUMENTACJI TECHNICZNEJ PRZYJĘTEJ W DZIAŁANIU TP
1. Zatwierdzona dokumentacja projektowa i techniczna TP 2. Wykonawcza dokumentacja techniczna TP (lub wykaz odstępstw od projektu) 3. Działa ukryte prace 4. Schemat pętli uziemienia i urządzeń uziemiających 5. Protokoły pomiaru rezystancji pętli uziemienia 6. Fabryczna dokumentacja techniczna urządzeń uzupełniających podstację transformatorową (w tym karty danych technicznych głównych urządzeń elektrycznych) 7. Protokoły ustawienia , pomiar i testowanie wyposażenia elektrycznego podstacji transformatorowej; realizowanych przez organizację budowlano-montażową 8. Czynność wydzielenia TP według bilansu i ex- 9. Czynność montażu dachu 10. Inwentaryzacja urządzeń elektrycznych 11. Wykazy sprzętu przeciwpożarowego i ochronnego TPDODATEK 10
PASZPORT EKSPLOATACYJNY TP
wspólne dane
Nazwa |
Data uruchomienia | Przynależność do salda | Główny konsument | 1 | 2 | 3 | Wskaźniki niezawodności konsumenta | 1 | 2 | 3 | Sezonowość konsumenta | 1 | 2 | 3 | Przewód zasilający | Główny | rezerwa |
Numer seryjny. |
Moc |
Łączenie grupy |
Pozycja Anzapfa |
Data nagrania |
Kierownik OZE | |||
Skompilowany | №№ | ||
w kratę | TP | ||
Sporządzono paszport | |||
Kierownik OZE | |||
Skompilowany | №№ | Karta inwentaryzacyjna środków trwałych | |
w kratę | TP | ||
Sporządzono paszport | |||
„_____” _______________ 19___ |
TC/odłącz obwód |
transformatory |
Ograniczniki przepięć 10 i 0,4 kV |
wynik pomiaru |
Nr przelewu |
wynik pomiaru |
wynik pomiaru |
wynik pomiaru |
zakończył. |
zakończył. |
zakończył. |
zakończył. |
DODATEK 11
KARTA TYPOWEGO SCHEMATU ELEKTRYCZNEGO TP (PRZYKŁAD WYPEŁNIENIA DLA PTS 10/0,4 kV, 25 kVA)
pryncypialny Schemat obwodu |
Nazwa urządzenia |
prąd znamionowy, A |
ilość szt. |
Odłącznik | Wyładowarka | Bezpiecznik | Transformator | Licznik | przełącznik noża | Wyładowarka | Opór | Przełącznik | Lampa | Bezpiecznik | Gniazdo wtykowe | Przełącznik | Przekładnik prądowy | Bezpiecznik | Przełącznik | Przekaźnik pośredni | Automatyczny przełącznik. | Automatyczny przełącznik. | Automatyczny przełącznik. | Automatyczny przełącznik. | Wyłącznik krańcowy | Fotoodporność | Izolacja się rozłączy. | Izolacja się rozłączy. | tuleja |
Nazwa urządzenia |
Schemat rewizji na dzień: w TP nr |
Odłącznik | Wyładowarka | Bezpiecznik | Transformator | Licznik | przełącznik noża | Wyładowarka | Opór | Przełącznik | Lampa | Bezpiecznik | Gniazdo wtykowe | Przełącznik | Przekładnik prądowy | Bezpiecznik | fotoprzekaźnik | Przełącznik | Przekaźnik pośredni | Przełącznik automatyczny 1 | Przełącznik automatyczny 2 | Przełącznik automatyczny 3 | Przełącznik automatyczny 4 | Wyłącznik krańcowy | Fotoodporność | Izolacja odłącznika | Jednostka napędowa | tuleja | Odstępstwa od standardowego projektu |
DODATEK 12
KARTA KONTROLNA TS 6-10/0,4 kV
OZE ___________________ Obszar nadrzędny ____________________________________ Miejscowość ________________________________________________________________ Rodzaj inspekcji __________________________________________________________________ (regularny, nadzwyczajny) ________________________________________________________________________________ ________________________________________________________________________________ ________________________________________________________________________________ Numer stacji transformatorowej 6-10/0,4 kV Nazwa usterki Uwaga _____________________________________________________________________________ _____________________________________________________________________________ _____________________________________________________________________________ Kontrola przeprowadzona przez ____________________________________ Karta kontroli zaakceptowana przez ___________________DODATEK 13
WYKAZ POMIARÓW PRĄDÓW OBCIĄŻENIOWYCH I ZWARCIOWYCH I NAPIĘCIOWYCH TS 6-10/0,4 kV
______________ TP OZE Nr ________________ tr-r Nr _____________________
Data i godzina pomiaru |
Prąd zwarciowy, kA |
Napięcie, V |
na wejściach tr-ra 0,4 kV |
na szynach rozdzielczych 0,4 kV |
u odległego konsumenta |
nazwa konsumenta |
DODATEK 14
Formularz strony tytułowejDZIENNIK REJESTRACJI WYNIKÓW BADAŃ SPRZĘTU TS 6-10/0,4 kV
______________________ OZE TP 6-10 / 0,4 kV_______________ Forma numeru dyspozytorskiego strony o mocy ___________ tys. kV × AWyniki pomiarów i testów
1. Transformator mocy
Data pomiarów, testów |
Numer fabryczny |
Rezystancja izolacji, MOhm |
Stan żelu krzemionkowego |
Wniosek, podpis |
instalacje |
Obudowa VN |
HH-przypadek |
|||||||
Data pomiarów, testów |
Wniosek, podpis |
Napięcie wsteczne, kV |
Aktywny opór element MOhm |
Napięcie przebicia, kV |
|||||||||||||
Data pomiarów, testów |
Aparatura rozdzielcza 6-10 kV |
Aparatura rozdzielcza 0,4 kV |
Pętla uziemienia |
Test, kV |
zakończenie, podpis |
Test, kV |
zakończenie, podpis |
opór |
zakończenie, podpis |
Główny |
pomocniczy |
Główny |
pomocniczy |
DODATEK 15
DZIENNIK USTEREK TS 6-10/0,4 kV
TPP _______ OZE ________________________________ Działka ________________________ Rozliczenie __________________ Forma strony
Rodzaj inspekcji (kontrola), data |
Główne zadania konserwacyjne rozdzielnice(RU) to: zapewnienie określonych trybów pracy i niezawodności sprzętu elektrycznego, przestrzeganie ustalonej procedury przełączania operacyjnego, monitorowanie terminowej realizacji zaplanowanych i zapobiegawczych prac.
Niezawodność pracy zazwyczaj charakteryzuje się określonymi uszkodzeniami na 100 połączeń. Obecnie dla rozdzielnicy 10 kV wskaźnik ten kształtuje się na poziomie 0,4. Najbardziej zawodnymi elementami rozdzielnicy są łączniki z napędem (od 40 do 60% wszystkich uszkodzeń) i odłączniki (od 20 do 42%).
Główne przyczyny uszkodzeń: pękanie i nakładanie się izolatorów, przegrzewanie się połączeń stykowych, pękanie napędów, uszkodzenia spowodowane nieprawidłowym działaniem personelu serwisowego.
Inspekcję rozdzielnicy bez wyłączania należy przeprowadzić:
w obiektach ze stałym personelem dyżurnym – co najmniej 1 raz w ciągu trzech dni,
w obiektach bez stałego personelu dyżurnego - przynajmniej raz w miesiącu,
w punktach transformatorowych - co najmniej 1 raz w ciągu 6 miesięcy,
Rozdzielnica o napięciu do 1000 V - nie rzadziej niż 1 raz na 3 miesiące (w KTP - co najmniej 1 raz na 2 miesiące),
po przerwaniu zwarcia.
Podczas kontroli sprawdź:
odpowiednie oświetlenie i sieci uziemiające,
dostępność sprzętu ochronnego
poziom i temperatura oleju w maszynach olejowych, brak wycieków oleju,
stan izolatorów (zapylenie, obecność pęknięć, wyładowań),
stan styków, integralność plomb liczników i przekaźników,
serwisowalność i właściwa pozycja wskaźniki położenia przełącznika,
działanie systemu alarmowego
prawidłowe ogrzewanie i wentylacja,
stan lokalu (przydatność drzwi i okien, brak przecieków w dachu, obecność i użyteczność zamków).
Nieplanowane przeglądy otwartych rozdzielnic przeprowadzane są w niesprzyjających warunkach atmosferycznych - gęsta mgła, lód, zwiększone zanieczyszczenie izolatorów. Wyniki kontroli są zapisywane w specjalnym dzienniku w celu podjęcia działań w celu wyeliminowania zidentyfikowanych wad.
Oprócz przeglądów sprzęturozdzielnica podlega kontrolom prewencyjnym i testom wykonywanym zgodnie z PPR. Zakres wykonywanych czynności jest uregulowany i obejmuje szereg czynności ogólnych oraz prace indywidualne specyficzne dla tego typu sprzętu.
Do ogólnych należą: pomiar rezystancji izolacji, sprawdzenie nagrzewania się skręcanych połączeń stykowych, pomiar rezystancji styków prąd stały. Specyficzne są kontrole czasu i przebiegu ruchomych części, charakterystyka wyłączników, działanie mechanizmu swobodnego wyzwalania itp.
Połączenia stykowe są jednym z najbardziej wrażliwych miejsc w rozdzielnicach. Stan połączeń stykowych określa się na podstawie oględzin zewnętrznych, a podczas badań prewencyjnych - za pomocą specjalnych pomiarów. Podczas oględzin zewnętrznych zwraca się uwagę na kolor ich powierzchni, odparowywanie wilgoci w czasie deszczu i śniegu, obecność poświaty i iskrzenia styków. Testy prewencyjne obejmują sprawdzenie nagrzewania się połączeń śrubowych za pomocą wskaźników termicznych.
Zasadniczo używana jest specjalna folia termiczna, która ma czerwony kolor, gdy normalna temperatura, wiśnia - w temp. 50 - 60°C, wiśnia ciemna - w temp. 80°C, czarna - w temp. 100°C. W temperaturze 110°C przez 1 h ulega zniszczeniu i przybiera jasnożółty kolor.
Folię termiczną w postaci kółek o średnicy 10 – 15 mm lub pasków nakleja się w kontrolowanym miejscu. Jednocześnie powinien być wyraźnie widoczny dla personelu operacyjnego.
Szyny zbiorcze rozdzielnic 10 kV nie powinny nagrzewać się powyżej 70 °C przy temperaturze otoczenia 25 °C. Od niedawna do kontroli temperatury złączy stykowych zaczęto stosować termometry elektryczne oparte na rezystancji termicznej, świece termiczne, kamery termowizyjne i pirometry (działają na zasadzie wykorzystania promieniowania podczerwonego).
Pomiar rezystancji styków połączeń stykowych przeprowadza się dla opon przy prądzie większym niż 1000 A. Praca jest wykonywana na odłączonym i uziemionym sprzęcie za pomocą mikroomomierza. Jednocześnie rezystancja odcinka opony w miejscu styku nie powinna przekraczać rezystancji tego samego odcinka (na długości i przekroju) całej opony o więcej niż 1,2 razy.
Jeżeli połączenie stykowe jest w stanie niezadowalającym, jest ono naprawiane, przez co jest demontowane, oczyszczane z tlenków i zanieczyszczeń oraz pokrywane specjalnym smarem antykorozyjnym. Dokręcanie odbywa się za pomocą regulowanego klucza dynamometrycznego, aby uniknąć deformacji.
Pomiar rezystancji izolacji przeprowadza się dla izolatorów podwieszanych i wsporczych megaomomierzem do 2500 V, a dla obwodów wtórnych i aparatury rozdzielczej do 1000 V megaomomierzem do 1000 V. Izolację uważa się za normalną, jeśli rezystancja każdego izolatora wynosi co najmniej 300 MΩ, a rezystancja izolacji obwodów i urządzeń wtórnych Rozdzielnica do 1000 V - nie mniej niż 1 MΩ.
Oprócz pomiaru rezystancji izolacji, podtrzymujące izolatory jednoelementowe są testowane napięciem o podwyższonej częstotliwości sieciowej przez 1 min. Do sieci niskiego napięcia napięcie testowe 1 kV, w sieciach 10 kV - 42 kV. Kontrola izolatorów wieloelementowych odbywa się w dodatniej temperaturze otoczenia za pomocą pręta pomiarowego lub pręta ze stałą iskiernikiem. Do odrzucenia izolatorów stosuje się specjalne tabele rozkładu napięcia na girlandze. Izolator jest odrzucany, jeśli ma napięcie mniejsze niż dopuszczalne.
Podczas pracy na powierzchni izolatorów odkłada się warstwa zanieczyszczeń, która przy suchej pogodzie nie jest groźna, ale staje się przewodząca w mżącym deszczu, mgle, mokrym śniegu, co może prowadzić do zachodzenia na siebie izolatorów. Do eliminacji sytuacje awaryjne izolatory są okresowo czyszczone poprzez przetarcie ręczne, przy użyciu odkurzacza oraz drążone pręty wykonane z materiału izolacyjnego ze specjalną końcówką w postaci kręconych szczotek.
Do czyszczenia izolatorów na otwartej rozdzielnicy należy używać strumienia wody. Aby poprawić niezawodność izolatorów, ich powierzchnię traktuje się hydrofobowymi pastami o właściwościach hydrofobowych.
Główne uszkodzenia rozłączników to spalenie i spawanie układu styków, awaria izolatorów, napędu itp. W przypadku stwierdzenia oznak spalenia styki są czyszczone lub usuwane, wymieniane na nowe, śruby i nakrętki na napędzie i innych miejsca są zaostrzone.
Podczas regulacji odłączników trójbiegunowych sprawdzana jest jednoczesność załączania noży. Przy prawidłowo wyregulowanym odłączniku nóż nie powinien sięgać do ogranicznika nakładki stykowej o 3 - 5 mm. Siła wyciągania noża ze styku stałego musi wynosić 200 N przy włączonym odłączniku prądy znamionowe 400 ... 600 A i 400 N - dla prądów 1000 - 2000 A. Części trące rozłącznika pokryte są smarem niezamarzającym, a powierzchnia styku neutralną wazeliną z domieszką grafitu.
Podczas kontroli przełączników oleju sprawdzane są izolatory, pręty, integralność membrany zaworu bezpieczeństwa, poziom oleju, kolor folii termicznych. Poziom oleju musi mieścić się w dopuszczalnych wartościach na skali wskaźnika poziomu. Jakość styków uważa się za zadowalającą, jeśli ich rezystancja styku odpowiada danym producenta.
Podczas kontroli przełączników olejowych należy zwrócić uwagę na stan końcówek prętów stykowych, integralność elastycznych kompensatorów miedzianych, prętów porcelanowych. W przypadku zerwania jednego lub więcej prętów, przełącznik jest natychmiast wyjmowany do naprawy.
Nieprawidłowe temperatury nagrzewania styków łukowych powodują ciemnienie oleju, wzrost poziomu oleju i charakterystyczny zapach. Jeżeli temperatura zbiornika wyłącznika przekroczy 70 °C, również jest on wyprowadzany do naprawy.
Najbardziej uszkodzonymi elementami wyłączników olejowych są ich napędy. Awarie napędu występują z powodu błędów w obwodach sterujących, niewspółosiowości mechanizmu blokującego, błędów ruchomych części i uszkodzenia izolacji cewki.
Bieżąca naprawa rozdzielnicy jest przeprowadzana w celu zapewnienia sprawności sprzętu do następnej zaplanowanej naprawy i zapewnia przywrócenie lub wymianę poszczególnych elementów i części. Wyremontować wykonywane w celu przywrócenia pełnej funkcjonalności. Odbywa się to z wymianą dowolnych części, w tym podstawowych.
Bieżący remont rozdzielnicy o napięciach powyżej 1000 V jest wykonywany w miarę potrzeb (w terminach ustalonych przez głównego inżyniera elektrowni). Remonty wyłączników olejowych przeprowadza się raz na 6 - 8 lat, rozłączników i rozłączników - raz na 4 - 8 lat, separatorów i zwieraczy - raz na 2 - 3 lata.
Remonty bieżące rozdzielnic o napięciu do 1000 V przeprowadza się co najmniej raz w roku w otwartych stacjach transformatorowych i po 18 miesiącach w zamkniętych stacjach transformatorowych. Jednocześnie monitorowany jest stan zakończeń, usuwany jest kurz i brud, wymieniane są izolatory, naprawiane są opony, dokręcane są połączenia stykowe i inne elementy mechaniczne, naprawiane są obwody sygnalizacji świetlnej i dźwiękowej oraz pomiary i przeprowadzane są testy ustanowione przez normy.
Remont rozdzielnicy o napięciu do 1000 V przeprowadza się co najmniej 1 raz na 3 lata.